Original publication: Blankenship, K., & Manuel, J. (2025). Two-Coat Inorganic Coating System for Steel Bridges. Transportation Research Record, 0(0). https://doi.org/10.1177/03611981241292586.
Abstract
Design considerations for steel bridge coatings include exposure environment, aesthetics, application, and cost. Steel bridge coatings must offer protection against corrosion. Current techniques include traditional three-coat zinc, epoxy, urethane systems, galvanizing, and thermal spray metallization. Another pathway for steel protection includes the use of decades-old inorganic zinc spray-applied coatings. This approach offers the performance of a metallized coating while using conventional spray application. What's new is the use of an inorganic topcoat that maintains performance and shop throughput while adding color and aesthetics. This study will compare a two-coat inorganic coating system alongside galvanized, thermal spray metallizing, and sealed thermal spray metallizing systems in corrosion resistance lab testing. A discussion of applied cost and throughput will be presented, along with a review of the chemistry of this approach and the sustainability benefits it offers.
Table of Contents
Introduction
Steel is a critical material for the world's infrastructure. It offers many design benefits to the engineer when compared to concrete. The major challenge for steel as a construction material is corrosion. Corrosion protection for steel bridges remains an area of interest and continued study. Painting, metallizing, and galvanizing remain the core options for corrosion protection. Weathering steel has successfully been used for decades. Understanding the corrosivity of the environment is key when specifying this type of corrosion protection. Stainless steel and duplex stainless steel are also seeing acceptance but at a slower pace due primarily to upfront cost.
TABLE 1 Various Testing Standards for Bridge Paints
Standard | Description | Category |
---|---|---|
ASTM B117 | Salt Fog | Performance |
ASTM D5894 | Cyclic Corrosion | Performance |
AASHTO R-31-09 Test 7 | Coating Identification | Quality Control |
ASTM D4541, D3359 | Adhesion | Performance, Quality of Application |
RCSC Appendix A | Slip Coefficient | Performance |
NEPCOAT QPL | Field History | Performance |
SSPC Paint 20 | Zinc-Rich Coating | |
ASTM D4417 | Test Method for Field Measurement of Surface Profile of Blast-Cleaned Steel | Quality of Application |
ASTM D4940 | Test Method for Conductimetric Analysis of Water-Soluble Ionic Contamination of Blast-Cleaning Abrasives | Quality of Application |
ASTM D7393 | Practicing for Indicating Oil in Abrasives | Quality of Application |
SSPC-SP 6 and 10 | Practice for Indicating Oil in Abrasives | Quality of Application |
Paint manufacturers develop paints and coatings in laboratories using several standard test methods beyond what is listed above. Testing is done against known controls, and often, lab-accelerated testing is run in parallel with real-world ageing tests. Development also includes application testing to mimic what happens at a fab shop and in the field. Once a paint is developed and offered to the market, it will typically be further qualified by DOTs or other outside organizations.
Today, the most common bridge paint system is a three-coat, liquid-applied system consisting of a zinc-rich primer, epoxy intermediate, and a urethane topcoat. As lead was regulated out of paint in the 1970s and 80s, zinc-rich paints gained a foothold. It should be noted that zinc paints have a much longer history starting in 1840 when a British gentleman named Robert Mallet presented a paper to the British Association for the Advancement of Science. He was granted a patent on the use of zinc in paint on iron in 1841 (1). In 1937 the first zinc paint was patented. The first commercial application of record occurred in 1938 (2). The earliest type of self-curing zinc-rich paint was patented in 1962 (3). Applications of single-coat inorganic zinc have been used for decades on structural steel, including the NASA Vertical Assembly Building constructed in 1964, shown in Figure 1 (4).
Figure 1 NASA Vertical Assembly Building (photo courtesy of NASA)
Single-coat inorganic zinc coatings have been used on several bridges dating back to 1993 and 1994 (Missouri and Virginia DOTs, respectively) (2).
The first zinc-rich paints were based on inorganic binder chemistry, namely silicates. Unlike most common paints (urethanes, epoxies, etc.) that are based primarily on carbon atoms, inorganic zinc paints are composed of silica, oxygen, and zinc (5). The film formation occurs as solvent evaporates, silicates hydrolyze through increasing exposure to atmospheric moisture. (5) The silicates may react with zinc and the iron substrate itself, creating excellent adhesion. High loading of zinc, the potential of some complexing of zinc and iron with the silicates, and the relatively permeable final film (allowing electrolyte passage) all contribute to the excellent cathodic protection offered by inorganic zinc paints. In fact, often, the addition of organic paints on top of inorganic zinc reduces performance against corrosion, as shown in Figure 2.
Figure 2 Single-Coat Inorganic Zinc (left) and Inorganic Zinc- Epoxy- Urethane (right) after 8 Years at the Kennedy Space Center Beachside Corrosion Test Site (6)
Single coat inorganic zinc primer has exceptional performance against corrosion, but only recently achieved wide recognition as a worthwhile option for steel bridge protection. In 2023, the National Steel Bridge Alliance authored a synthesis paper on Single Coat Inorganic Zinc Protection for Steel Bridges (7). One reason for this lack of enthusiasm could be the perception that organic zinc-rich primers are easier to use, especially compared to inorganic zinc. Organic zinc primers tend to have more surface tolerance and are not as sensitive to atmospheric humidity for cure. They allow for quick application of the midcoat and topcoat. Inorganic zinc primers do require humidity for cure and need a longer topcoat window for full cure. Also, urethanes that are used as topcoats come in a range of gloss and color. Inorganic zinc primers are matte and limited to variations of gray.
In an effort to offer extended corrosion protection without the slower throughput and lack of color, a system based on an all-inorganic, two-coat system has been developed. This system starts with an inorganic zinc primer and is top-coated with an inorganic finish, as shown in Figure 3.
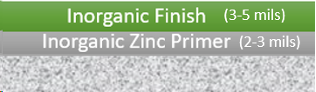
Figure 3 Illustration of Two-Coat Inorganic Corrosion Protection System on Steel
The finish can be applied within hours of primer application because it is composed of similar resin chemistry. Also, the finish does not contain zinc dust and consequently can be pigmented to various matte colors. While the typical three-coat system offers a 20-30 year service life (8), single-coat and two-coat inorganic systems offer well beyond that. This extended service life places them alongside other long-life corrosion protection systems such as galvanizing and thermal spray metalizing.
As noted earlier, assessing performance of long-life corrosion protection systems for steel continues to be a debated challenge. When reviewing standards for galvanizing and thermal spray metallizing, it is difficult to find any true performance assessments other than predictive life-cycle calculations. Most of the related standards and techniques revolve around preparation and application (Table 2).
TABLE 2 Standards for Galvanizing and Thermal Spray Metalizing
Standard | Description | Category |
---|---|---|
ASTM A123 | Spec for HDG Coating of Iron and Steel | Quality of Application |
ASTM A143 | Practice for Safeguarding Against Embrittlement (HDG) | Quality of Application |
ASTM A384 | Practice for Safeguarding Against Warpage and Distortion (HDG) | Quality of Application |
ASTM A385 | Practice for Providing High-Quality Zinc Coatings | Quality of Application |
SSPC-CS 23.00 | Spec for the Application of Thermal Spray Coatings (Metallizing) of Aluminum, Zinc, and Their Alloys and Composites for the Corrosion Protection of Steel | Quality of Application |
SSPC-QP 6 | Procedure for Evaluating the Qualification of Contractors Who Apply Thermal Spray | Quality of Application |
ASTM A780 | Practice for Repair of Damaged and Uncoated Areas of HDG Coatings | Quality of Application |
ASTM E376 | Practice for Measuring Coating Thickness | Quality of Application |
ASTM B 117 Salt Fog testing has been used for decades to test paints and coatings for their resilience against corrosion. The salt fog test is a constant fog of neutral salt (5% NaCl) at 35 degrees Celsius. The test panels typically are scribed, exposing bare steel, and are tested over the course of hundreds or thousands of hours. While this test has not been sufficiently correlated to real-world ageing (9), it does offer the formulator a powerful screening tool for identifying prototypes that will likely offer corrosion protection properties. Figure 4 shows results of a two-coat inorganic system after 14,954 hrs salt fog testing.
Figure 4 Two-Coat Inorganic System after 14,954 hrs Salt Fog (Courtesy MoDOT)
As galvanizing and thermal spray metalizing have entered the market as viable, long-life corrosion protection systems, continuous salt fog tests have been scrutinized. The critique primarily resides around the applicability to what is observed in the real world. Aside from coastal environments, salt exposure is typically intermittent. Various cycle tests have since been introduced to address this, including ASTM D5894, SAE J2334, NORSOK Standard M-501, and ISO 12944-9 Annex B Cyclic Ageing.
For this study, the "ISO 12944-9 (2018) Paint and varnishes- Corrosion protection of steel structures by protective paint system- Part 9: Protective paint systems and laboratory performance test method for offshore and related structures" was used. This test is recognized around the world as a suitable standard to identify coating systems that perform in harsh offshore environments where high corrosivity is present (10). Currently, several three-coat systems meet the requirement of ISO 12944-9 CX classification. The standard requires no blistering, rusting, cracking, flaking, and a maximum of 3.0mm scribe creep after 4200 hours of cyclic ageing. A passing example of panels coated with a three-coat system based on an inorganic zinc silicate primer, epoxy midcoat, and polyurethane topcoat is shown in Figure 5.
Figure 5 Three-Coat IOZ/Ep/PU System Passing ISO 12944-9 CX
Figure 6 shows a passing example of panels coated with an organic zinc primer, epoxy midcoat, and polyurethane topcoat.
Figure 6 Three-Coat IOZ/Ep/PU System Passing ISO 12944-9 CX
As referenced earlier, a three-coat system is typically regarded to offer 20-30 years service life. The ISO 12944-9 CX test may approximate the conditions needed for degradation after 25 years. Global environments are highly variable, but this test approximates a highly corrosive environment.
METHODS
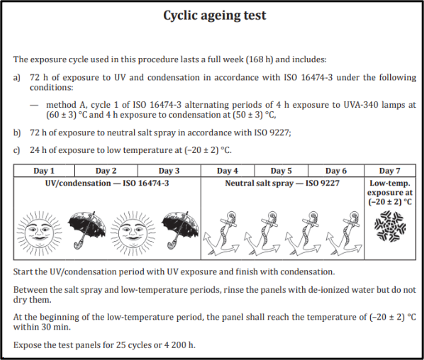
The Annex B Cyclic Ageing test found in ISO 12944-9 includes the exposure cycle shown in Figure 7.
Figure 7 ISO 12944-9 Cyclic Ageing Cycle Description
This study was run for 25 cycles, taking 4,200 hours per the ISO 12944-9 standard. The passing result indicates the coating system will provide at least 25 years of service before its first maintenance. Additional cycles are not officially recognized by the standard but are only planned for information and comparison purposes.
Description of Systems Tested
Five corrosion protection systems were tested by an outside, independent laboratory: a two-coat inorganic system, a low-VOC two-coat inorganic system, galvanizing, thermal spray metallizing, and thermal spray metallizing with a urethane clear sealer. Table 3 describes the samples.
TABLE 3 Corrosion Protection Systems
System ID | Panel ID | Description | DFT Coat 1 | DFT Coat 2 | Cure |
---|---|---|---|---|---|
A | 40A | Low-VOC Inorganic Zn Primer/Low-VOC | 2.8 | 3.6 | Minimum 7 days ambient |
A | 44B | Low-VOC Inorganic Zn Primer/Low-VOC | 3.4 | 2.8 | Minimum 7 days ambient |
A | 48B | Low-VOC Inorganic Zn Primer/Low-VOC | 3.3 | 3.1 | Minimum 7 days ambient |
A | 61B | Low-VOC Inorganic Zn Primer/Low-VOC | 3.3 | 4.2 | Minimum 7 days ambient |
A | 62B | Low-VOC Inorganic Zn Primer/Low-VOC | 3.0 | 5.1 | Minimum 7 days ambient |
B | 4B | Inorganic Zn Primer/Inorganic Finish | 2.6 | 3.6 | Minimum 7 days ambient |
B | 5B | Inorganic Zn Primer/Inorganic Finish | 2.7 | 3.6 | Minimum 7 days ambient |
B | 6B | Inorganic Zn Primer/Inorganic Finish | 2.9 | 4.4 | Minimum 7 days ambient |
B | 7A | Inorganic Zn Primer/Inorganic Finish | 2.5 | 3.8 | Minimum 7 days ambient |
B | 9B | Inorganic Zn Primer/Inorganic Finish | 2.8 | 4.7 | Minimum 7 days ambient |
C | 1 | Hot-Dipped Galvanizing | 3.3 | ---- | ---- |
C | 6 | Hot-Dipped Galvanizing | 3.4 | ---- | ---- |
C | 7 | Hot-Dipped Galvanizing | 3.6 | ---- | ---- |
C | 10 | Hot-Dipped Galvanizing | 3.4 | ---- | ---- |
C | 13 | Hot-Dipped Galvanizing | 3.5 | ---- | ---- |
D | 1 | Thermal Spray Metallizing | 13.8 | ---- | ---- |
D | 3 | Thermal Spray Metallizing | 14.0 | ---- | ---- |
D | 7 | Thermal Spray Metallizing | 12.4 | ---- | ---- |
D | 9 | Thermal Spray Metallizing | 13.3 | ---- | ---- |
D | 10 | Thermal Spray Metallizing | 13.0 | ---- | ---- |
E | 1 | TSM/Urethane Sealer | 19.0 | 19.0 | Minimum 7 days ambient |
E | 6 | TSM/Urethane Sealer | 22.0 | 22.0 | Minimum 7 days ambient |
E | 9 | TSM/Urethane Sealer | 18.0 | 18.0 | Minimum 7 days ambient |
E | 10 | TSM/Urethane Sealer | 19.8 | 19.8 | Minimum 7 days ambient |
E | 11 | TSM/Urethane Sealer | 20.1 | 20.1 | Minimum 7 days ambient |
Preparation of Galvanized and Thermal Spray Metallizing Panels
Hot-dipped galvanized panels were prepared according to ISO 1461. Application of galvanizing was on carbon steel panels with an MEK wash prior to application. Thermal spray metallizing panels were prepared according to ISO 2063 with 100% zinc. Application of thermal spray metal was on ASTM A36 carbon steel panels with a surface prep of G50 grit blast to SSPC-SP5 with a 1-3 mil anchor profile.
Application of Painted Samples
Painted samples were spray-applied to ASTM A36 carbon steel with a surface prep of G50 grit blast to SSPC-SP5 with a 1-3 mil anchor profile. Spray application utilized airless spray (60:1) with a 517 tip. Pressures varied between the various coatings ranging from 2,000 to 2,500 psi.
Additional Conditions
Table 4 highlights additional details surrounding the conditions around sample panel preparation. Environmental conditions and time to test are of particular note. Inorganic silicates cure with moisture in the atmosphere. Relative humidity is an important variable to factor when using this coating chemistry. Also, age of the panel when tested is of consideration as all of the systems tested use reactive zinc metal. As the coating ages zinc will react with atmosphere and form corrosion products. The degree of this reaction may have an impact on final performance. As all systems were applied and tested by an outside lab, conditions were not necessarily kept controlled.
TABLE 4 Additional Application Conditions
System | Temp. (Degrees Celsius) | % RH | Days Prime to Topcoat | Days Application to Test |
---|---|---|---|---|
System A | Primer, 22.5; Topcoat, 24 | Primer, 24; Topcoat, 27 | 3 | 33 |
System B | Primer, 24.5; Topcoat, 29.5 | Primer, 42; Topcoat, 42 | 1 | 27 |
System C | 21 days elapsed from receipt of galvanized panels to test start | |||
System D | 2 days elapsed from receipt of metallized panels to test start | |||
System E | 11 days elapsed from receipt of sealed metallized panels to start of test |
RESULTS
ISO 12944-9 Annex B Cyclic Ageing rates panels on blistering, rusting, cracking, and flaking. It also requires a measurement of scribe creep. Scribe creep was assessed and measured based on the visible rust observed at the scribe. Since the ISO 12944-9 standard requires an assessment for measurement under the scribe, the scribe creep should be considered an estimate. The passing requirement for ISO 12944 CX is shown in Table 5.
TABLE 5 ISO 12944-9 CX Passing Criteria
Blistering (ISO 4628-2) | Rusting (ISO 4628-3) | Cracking (ISO 4628-4) | Flaking (ISO 4628-5) | Scribe Creep* |
---|---|---|---|---|
0(S0) | Ri0 | 0(S0) | 0(S0) | < or = 3mm |
Corrosion under the scribe was not assessed after 4,200 hours as it is destructive. The panels were placed back into testing after the aforementioned assessments. Corrosion under the scribe will be analyzed at the conclusion of the 50 cycles or 8,400 hours testing. Results are listed in Table 6.
TABLE 6 Results of ISO 12944-9 Annex B Cyclic Ageing
*Estimated scribe creep, coating not removed as test is ongoing, **Stained from edge rust or grit contamination
System | Panel ID | Blistering (ISO 4628-2) | Rusting (ISO 4628-3) | Cracking (ISO 4628-4) | Flaking (ISO 4628-5) | Scribe Creep* |
---|---|---|---|---|---|---|
A | 40A | 0(S0) | Ri0** | 0(S0) | 0(S0) | 0.36 |
A | 44B | 0(S0) | Ri0 | 0(S0) | 0(S0) | 0.00 |
A | 48B | 0(S0) | Ri0** | 0(S0) | 0(S0) | 0.00 |
A | 61B | 0(S0) | Ri0** | 0(S0) | 0(S0) | 0.29 |
A | 62B | 0(S0) | Ri0 | 0(S0) | 0(S0) | 0.00 |
B | 4B | 0(S0) | Ri0 | 0(S0) | 0(S0) | 0.00 |
B | 5B | 0(S0) | Ri0 | 0(S0) | 0(S0) | 0.00 |
B | 6B | 0(S0) | Ri0 | 0(S0) | 0(S0) | 0.00 |
B | 7A | 0(S0) | Ri0 | 0(S0) | 0(S0) | 0.00 |
B | 9B | 0(S0) | Ri0 | 0(S0) | 0(S0) | 0.00 |
C | 1 | 0(S0) | Ri4 | 0(S0) | 0(S0) | 8.19 |
C | 6 | 0(S0) | Ri4 | 0(S0) | 0(S0) | 7.40 |
C | 7 | 0(S0) | Ri4 | 0(S0) | 0(S0) | 4.25 |
C | 10 | 0(S0) | Ri4 | 0(S0) | 0(S0) | 16.75 |
C | 13 | 0(S0) | Ri4 | 0(S0) | 0(S0) | 9.64 |
D | 1 | 0(S0) | Ri0 | 0(S0) | 0(S0) | 6.33 |
D | 3 | 0(S0) | Ri0 | 0(S0) | 0(S0) | 1.85 |
D | 7 | 0(S0) | Ri0 | 0(S0) | 0(S0) | 1.42 |
D | 9 | 0(S0) | Ri0 | 0(S0) | 0(S0) | 1.74 |
D | 10 | 0(S0) | Ri0 | 0(S0) | 0(S0) | 0.38 |
E | 1 | 2(S3) | Ri0 | 0(S0) | 0(S0) | 0.48 |
E | 6 | 2(S3) | Ri0 | 0(S0) | 0(S0) | 0.31 |
E | 9 | 2(S3) | Ri0 | 0(S0) | 0(S0) | 0.30 |
E | 10 | 2(S4) | Ri0 | 0(S0) | 0(S0) | 0.19 |
E | 11 | 2(S4) | Ri0 | 0(S0) | 0(S0) | 0.21 |
ISO standards use "0" to signify high-performance. For blistering, ISO uses the designation Density (Size) where, for density, 0 is none, 2 is few, and 5 is dense. For size, S0 is none, S1 is small, and S5 is large. Cracking is rated for quantity, 0 being none and 5 being many, and size from S0 where no cracks are visible under magnification of 10X, S1 is only visible under 10X, S2 is just visible with normal vision, S3 is clearly visible with normal vision, S4 is large cracks up to 1 mm wide, and S5 is very large cracks greater than 1mm wide. For flaking, ISO uses % flaking (size) where 0 is no flaking, 1 is 0.1%, 3 is 1%, and 5 is 15%. The flaking size scale starts at S0 under 10X magnification, S1 up to 1mm, S2 up to 3mm, S3 up to 10mm, S4 up to 30mm, and S5 larger than 30mm. Rusting is measured for % area and is rated as Ri0 being 0 rusted area, Ri1 being 0.05%, Ri3 being 1%, Ri4 being 8%, and Ri5 being 40%.
Photographs after the panels were removed from the 25 cycles of testing are shown in Figures 8 through 12.
DISCUSSION
The low estimated scribe creep indicates that the two-coat inorganic systems and the thermal spray metallizing systems offer continued cathodic protection overexposure, with the System B two-coat inorganic system showing no scribe creep on any of the five panels tested. None of the systems showed any cracking or flaking, and only the thermal spray metallizing system with the urethane sealer showed blistering. Field or plane rusting was not seen on the two-coat inorganic systems or the thermal spray metallizing systems. The low-VOC inorganic system did appear to have notable rusting at the scribe in two of the panels tested. Previous internal lab testing does not show this. It is not certain whether this variance is within the expected noise of the test or if it is indicative of a true performance difference between the low-VOC and the traditional inorganic system. Further testing will be performed to make a better assessment. The scribe creep measured is far below the allowable scribe creep for passing the test and significantly better than traditional three-coat, as shown in Figures 5 and 6.
It is theorized that the silicate binder allows complexing between the silicate binder, zinc, and iron substrate, allowing for excellent adhesion and contact of the zinc with the steel substrate. The very low to virtually no corrosion at the scribe seems to emphasize the cathodic protection afforded by this technology. This type of performance has been seen with single-coat inorganic zinc, but now it appears that an inorganic finish coat enables the same level of protection. Unlike organic epoxies and urethanes, the silicate-based inorganic finish maintains a level of vapor permeability that permits oxygen, water, and carbon dioxide to reach the outer layer of zinc particles within the zinc-rich primer layer. Zinc corrosion products will form over time and are thought to fill in any pores creating an impermeable layer or patina. The inorganic chemistry of the binder prevents it from degrading in UV exposure. The results of the ISO 12944-9 cyclic ageing test also suggest that the inorganic finish may help to maintain aesthetics by masking the corrosion products that are visible in the thermal spray metallizing panels.
Both the inorganic zinc-rich primer alone and the two-coat inorganic system of inorganic zinc-rich primer with the inorganic finish are rated class B for slip, meaning no roughening and no masking is required when installing with bolted connections. (Tested according to the Research Council on Structural Connections Specification for Structural Joints Using High-Strength Bolts, Appendix A. Class B Certificates are system and manufacturer-specific. Certificates are available upon request from Carboline.) Because inorganic finishes are based on the same inorganic resin as the inorganic zinc-rich primer, topcoating is possible within hours rather than days. Both of these factors improve schedule time compared to the traditional inorganic zinc-rich primer, epoxy, urethane system.
Inorganic coatings use different raw materials than organic coating systems that primarily rely on petroleum feedstocks. The cured silicate-based film is more glass or rock-like and is not thought to contribute to microplastics in the environment.
The galvanized panels exhibited notable rusting in the plane and the scribe. It is unclear if this can be attributed to the galvanizing process for these samples or whether the salt cycling is too aggressive to allow the proper mix of protective corrosion products to form on the outermost zinc layer.
While performance is paramount, cost and schedule are critical to a successful bridge project. Current three-coat system may utilize an inorganic or organic zinc-rich primer. Often, if the DOT or guiding specification allows, an organic zinc primer will be used. Overcoating an organic zinc primer with an epoxy midcoat can be done within the same day or shift even. Applying an organic epoxy midcoat over an inorganic zinc primer requires a minimum of 18-24 hour wait time in order to allow moisture curing of the inorganic zinc primer. In contrast, topcoating of the inorganic zinc primer with an inorganic finish can be done within two hours. The moisture permeability of the finish allows for continued cure of the primer after topcoating. This puts two-coat inorganic coating systems at an advantage over three-coat organic zinc-based systems.
When comparing painting to schedule for galvanizing and thermal spray metallizing, different factors should be considered. Typically, galvanizing is done outside of the fab shop, which can extend schedule depending on the availability and capacity of local galvanizers. Thermal spray metalizing can be done in the fab shop, so that is often not a consideration. What is of consideration is the longer cleaning cycle times used by fabricators to ensure a proper surface for thermal spray coating application.
When reviewing cost, many factors are to be considered. The NSBA published results of a cost survey at the 2020 World Steel Bridge Symposium (11). Using uncoated weathering steel as the baseline, the NSBA study calculated the following relative cost comparison. See Table 7.
TABLE 7 Cost Comparison of Corrosion Protection Systems
System | % Increase Over Uncoated Weathering Steel (Median) |
---|---|
Single-Coat Inorganic Zn | 6 |
Three-Coat OZ/Ep/PU | 13 |
Three-Coat IOZ/Ep/PU | 16 |
Hot-Dipped Galvanizing | 25 |
TSM, Sealed | 36 |
CONCLUSIONS
Two-coat inorganic systems are corrosion protection systems that may be applied in the shop or field like traditional three-coat systems. While some traditional three-coat systems can pass the ISO 12944-9 CX standard indicating 25 years time to first maintenance, the corrosion at the scribe is significant. The inorganic systems show much less corrosion at the scribe, indicating better corrosion protection. This study also showed one example of how galvanizing and metallizing compare when tested for long-term corrosion performance. Galvanizing and metallizing are accepted as long-term corrosion protection strategies. The results of this study suggest that inorganic systems should be considered to be in this class of corrosion protection strategies as well. While single-coat inorganic systems offer performance, the lack of color can be limiting for wider acceptance in the bridge market. This testing indicates that color is achievable without sacrificing performance by using an inorganic topcoat. Since the two-coat inorganic system is class B slip rated, application can be done without masking of faying surfaces. This saves time and money and virtually eliminates field painting once installed. Two-coat inorganic systems are worthy of consideration in the current class of long-life corrosion protection systems.
GPI Labs (data collection)
Midwest Thermal Spray (TSM sample prep)
V&S Galvanizing (HDG sample prep)
This work and all testing was funded by Carboline.
DECLARATION OF CONFLICTING INTERESTS
The author(s) declared no potential conflicts of interest with respect to the research, authorship, and/or publication of this article.
The authors confirm contribution to the paper as follows: study conception and design: J. Manuel; analysis and interpretation of results: K. Blankenship; draft manuscript preparation: K. Blankenship. All authors reviewed the results and approved the final version of the manuscript.
1. Tator, K. B. Zinc Rich Coatings. In ASM Handbook Organic Protective Coatings (Kenneth B. Tator, ed.), ASM International, Materials Park, OH, 2015, pp. 213.
2. Murphy, T., T. Hopper, and J. McConnell. Single Coat Inorganic Zinc Protection for Steel Bridges. National Steel Bridge Alliance and American Institute of Steel Construction, Chicago, IL, 2023., pp. 3.
3. Tator, K. B. Zinc Rich Coatings. In ASM Handbook Organic Protective Coatings (Kenneth B. Tator, ed.), ASM International, Materials Park, OH, 2015, pp. 214.
4. Carboline. Countdown: How Carbozinc 11 Helped Win the Space Race [Internet]. 2023. [cited 2024 Feb 7]. Available from: https://www.carboline.com/solution-spot/posts/countdown-how-carbozinc-11-helped-win-the-space-race.
5. Munger, C. G., Corrosion Prevention by Protective Coatings. NACE International, Houston, TX, 1999.
6. Murphy, T., T. Hopper, and J. McConnell. Single Coat Inorganic Zinc Protection for Steel Bridges. National Steel Bridge Alliance and American Institute of Steel Construction, Chicago, IL, 2023., pp. 10.
7. Murphy, T., T. Hopper, and J. McConnell. Single Coat Inorganic Zinc Protection for Steel Bridges. National Steel Bridge Alliance and American Institute of Steel Construction, Chicago, IL, 2023., pp. iii.
8. Texas DOT. Bridge Preservation Guide [Internet]. 2024 [cited 2024 May 7]. Available from: https://www.txdot.gov/business/resources/highway/bridge/bridge-publications.html.
9. Montgomery, E. L. Timescale Correlation Between Marine Atmospheric Exposure and Accelerated Corrosion Testing. Presented at the NACE Corrosion Conference and Expo, Houston, TX, 2011.
10. ISO 12944 (2018) Paint and varnishes- Corrosion protection of steel structures by protective paint system- Part 9: Protective paint systems and laboratory performance test method for offshore and related structures. ISO, Switzerland, 2018.
11. Carlson, J., Introduction to Modern Corrosion Protection Systems. Presented at the World Steel Bridge Symposium, Virtual, 2021.