Over the course of a tank car’s normal service, it is inevitable that its user will need to consider repairing its lining.
But when, whether, or how to do it is not always straightforward. A constellation of factors influence the nature and extent of damage to a lining. Building from that, the nature and extent of damage may require something other than a repair.
It’s a lot to unpack, but we’ve unpacked it here.
This is the final part of a three-part series on rail tank car linings. Part 1 covered lining product selection. Part 2 covered inspection of tank car linings.
Common reasons to repair a tank car lining
How to approach a tank car lining repair depends on the defect affecting the lining. The risk of a defect, or even the premature failure of a lining, can come from any of the following:
- • Unintended damage to the lining during loading, unloading, maintenance, or cleaning
- • Mechanical or chemical wear sustained in the normal service of the tank car
- • A flaw in the manufacture or application of the lining
The most common tank car lining defects an inspector might observe include:
Blistering - This bubble-like defect of the lining may emerge within or beneath the film of the lining. It can occur immediately after application or within days, weeks, or even months later. Blisters are typically caused by improper surface preparation, the presence of surface contaminants, solvent entrapment, incompatible service, extreme temperatures, or improper cleaning.
Cracking - The cracking of a tank car lining is usually found in areas subjected to flexing or other types of movement of the steel. This is normal and expected stress, so if cracking appears, the likely culprits are too-high film thickness or a poor profile achieved during surface preparation. In rarer cases, cracking can occur if the tank car shell sustains exceptionally harsh stress.
Mechanical damage – This physical damage to the tank car lining usually occurs during loading, unloading, maintenance, or cleaning. For instance, impacting the lining with hoses, ladders, tools, or cleaning apparatus are common causes of mechanical damage. Dislodging clogs or even inserting probes to assess cargo levels can also cause mechanical damage.
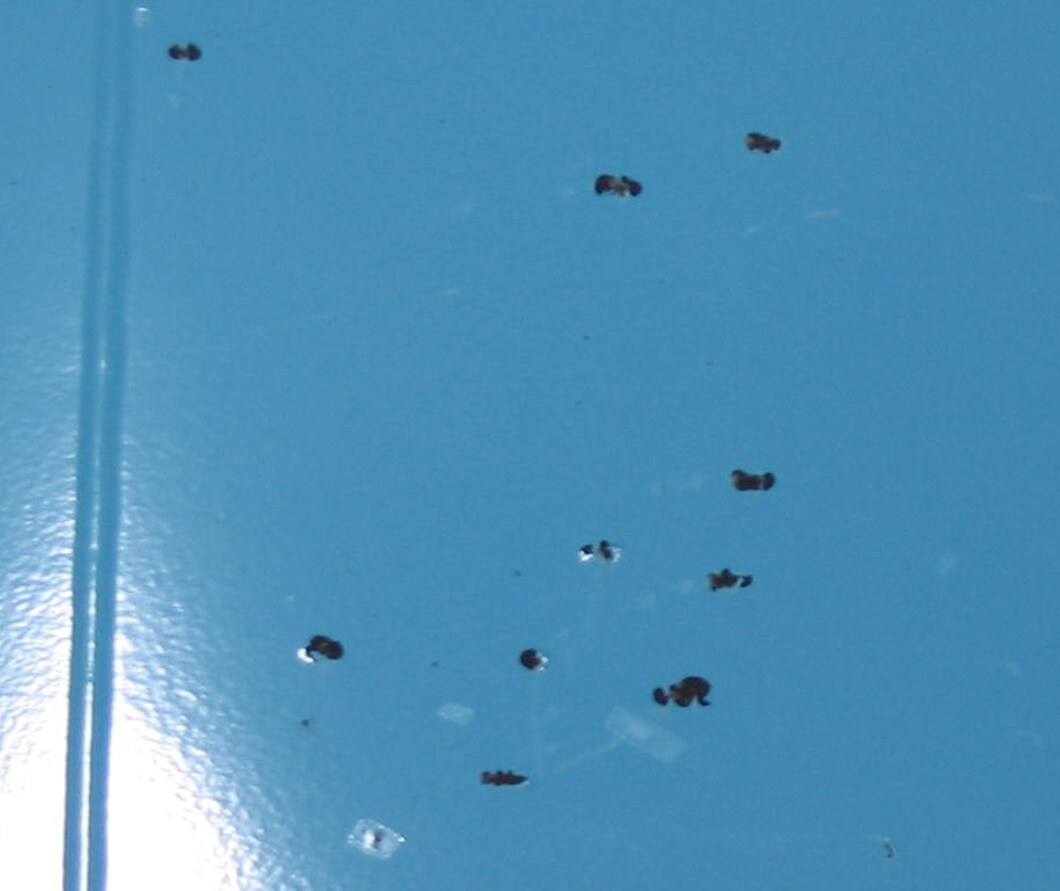
Off-ratio lining materials – If a tank car lining is a two-part system, the improper measurement or mix of parts A and B will prevent the lining from curing as intended. If that happens, cargo could stick to the lining. Two problems can follow: One, that portion of the lining may never cure and instead fail. Two, constituents of the uncured lining may leach into the commodity and render it unsaleable and useless.
Corrosion staining – This phenomenon occurs when a tank car lining is improperly applied, or when no lining is applied at all. For one example, corrosion staining is common if unlined or improperly lined tank cars haul highly acidic commodities. For another, it can occur if the specified lining is generally incompatible with the commodity. Expect to see corrosion stains form in the vulnerable areas of a tank car shell, including its safety valve, nozzle, threaded ports, or weld seams.
Commodity wear – A common vector of commodity wear damage is the impact of the lining by frozen cargoes. For example, 83% ammonium nitrate solution freezes at 150°F (65.5° C). Certain sulfur formulas freeze at around 194°F (90°C). If the temperature inside the tank drops below the freezing point of the commodity, the frozen chunks that form as a result can bang against the lining, causing it to chip.
All the scenarios above are common, but that doesn’t mean tank car operators should remain solely reactive to lining defects. The proactive search for process improvements is a low-cost, high-impact way to protect the condition of tank car linings and keep cars on the rails longer.
Tank car lining repair vs. relining
Once the extent and nature of defects have been defined following tank car lining inspection, the next step is to determine whether to repair the lining or replace it with a new one. Use the simple chart below as a starting point.
REPAIR OR RELINE | TYPE OF DEFECT | EXAMPLES |
---|---|---|
RELINE | Defects covering a large surface area or that will continue to spread |
|
REPAIR | Isolated defects that do not cover a significant area and will not continue to spread |
|
But there’s more nuance to the decision than merely assessing the size, amount, or severity of tank car lining defects. Consider these additional questions:
- • How old is the lining and what is its expected service life?
- • How old is the tank car?
- • When does the car's lease terminate?
- • When is the car due for requalification?
The answers may further justify a repair or a reline, but they may also point to a third way: If a tank car with a damaged lining is very old or is nearing its mandatory requalification, it may be sensible to do nothing and place the car into service carrying benign or inert cargo. Of course, this is only possible with larger or more flexible fleets.
Federal mandates for rail tank car maintenance
In the U.S., federal law mandates that tank car linings must receive periodic inspection or requalification when the hauled commodity has a corrosion rate exceeding 2.5 mils (64 microns) per year on mild steel. Most liquid commodities shipped by rail fall into this category, including chlorides, sulfides, fertilizer solutions, other oxidizing agents, and crude oils. In addition, the updated HM216B regulation expanded requirements for rail transport of hazardous commodities.
A periodic lining inspection is not required for commodities that are considered “non-corrosive,” such as glycols, corn sweeteners, solvents, and phenol. In these cases, inspections may be performed at the discretion of the tank car owner based on product purity requirements.
Because tank cars are considered a permit-required confined space according to 26 CFR 1926, an entry permit is required and the interior environment must be monitored for proper air quality.
Proper surface preparation for rail tank car linings
To ensure safe entry, a tank car must first be thoroughly cleaned to remove any contaminants from the substrate and achieve a neutral pH level. The extent of this cleaning process will depend upon the previous service and degree of coating failure. Even if a tank car appears clean, previous cargoes may have settled onto the substrate.
If this is the case, the substance must be removed to prevent contamination of the blast media, osmotic blistering, or interference with coating adhesion. The surface should also be tested for contaminants like oils and non-visible soluble salts, especially if the car carries acidic or alkaline commodities.
If additional cleaning or neutralization is required, the appropriate method will need to be repeated before the final blast is performed. Depending on the nature of the previous service, this may include prebaking, steam injection, hot water wash, or chemical cleaning.
Once the interior is clean, abrasive blasting to SSPC-SP 5/NACE No. 1 comes next. This may include vacuum blasting, open blasting, or power tool cleaning with a bristle blaster. Open blasting is not typically recommended for isolated repairs given the higher risk for collateral damage to the lining.
Next, the edges of the repair area must be feather sanded to reduce the film thickness. Based on the required film thickness, the blast profile may be specified at a minimum of 2 mils (51 microns) and as high as 4.5 mils (114 microns) depending on the product specified. For example, baked phenolics require a smoother blast profile of approximately 2 mils (51 microns). After interior blasting, the tank car must be cleaned of all debris, dust, and loose abrasive by vacuum or dry brush.
Application and curing process for tank car lining repair
For optimal performance, it is critical to follow the proper application and curing process. The lining should be applied according to the specified film thickness. For example, baked phenolics are applied at a dry film thickness of 5-8 mils (127-203 microns), while most epoxies are applied at 12-15 mils (305-381 microns) and vinyl esters and epoxy novolacs are applied at dry film thicknesses in excess of 20 mils (508 microns).
Carboline’s Plasite 9060 has been used rather extensively to repair tank cars lined with baked phenolics. A low-bake lining like Plasite 9085 is ideal for sulfuric acid immersion service, while Plasite 4550 S is used to repair linings for crude oil service both in the shop and in the field.
Our innovative burst pouch is also available for railcar linings like Plasite 9060, Plasite 9573, Plasite 9085, Carboguard 992, and Carboguard 995. Burst pouches are ideal for small repairs: They contain only 10 ounces (283 grams) of product, so applicators can easily use only the amount of product they need and avoid the needless cost of whole buckets of product and the time it takes to prepare them. Each of the pouches is filled with the exact right amount of product so that, once burst and properly mixed, there is zero risk of an improper mix ratio.
During application, it’s important to consider how ambient conditions will impact the curing process. Air-dry coatings such as epoxy novolacs can take several days to cure, especially during the winter months in colder climates. In such cases, repair shops opt for force cures to speed up the process.
In more recent years, mobile repair units have emerged that make field repairs of tank car linings more convenient. While this helps to reduce out-of-service time for a tank car, mobile repair units tend to lack the in-house baking capabilities that support force cures, often resulting in longer cure times depending on ambient conditions.
As a final step, a thorough inspection of the lining should be performed to verify that proper film thickness has been achieved and the coating is free of any holidays.
Depending on the service, haulers expect tank car linings to last a minimum of five to 10 years. However, if properly maintained and repaired over the course of its service life, an interior lining could provide decades of protection both to the tank car and its important cargo.