Legacy industry players and startups alike have poured significant resources, time, and energy into carbon capture and storage (CCS) and carbon capture, utilization, and storage (CCUS).
Though CCS and CCUS are far from perfected processes, their early innovators have demonstrated that they are sufficiently viable to pursue at scale.
Protective coating and lining manufacturers have a part to play in this pursuit. Now is the time to build knowledge of processes, equipment, and corrosion risks so that they can contribute to the long-term performance of CCS/CCUS assets.
The three principal CO₂ capture technologies are summarized below, and each is accompanied by descriptions of corrosion protection coatings and linings that we feel might be suitable for CCS/CCUS corrosion protection.
Pre-combustion capture
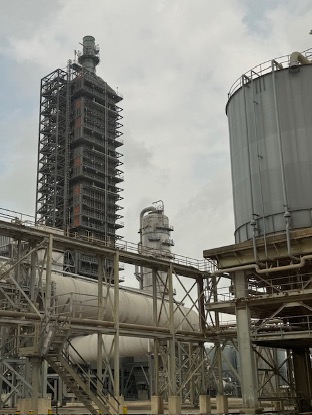
Pre-combustion capture separates CO₂ from a fuel prior to burning by exposing the fuel to steam and solvents at high pressure. The resulting gaseous byproduct consists mainly of carbon monoxide and hydrogen, a mixture known as syngas, which can be sold as fuel to industries or used within the plant.
Because the syngas production process occurs at temperatures often exceeding 2,500°F (1,371°C), any needed corrosion protection would likely be achieved using specialty alloy steels in process equipment and not a resinous coating or lining.
But adjacent assets that support that process include glycol solvent tanks and the curbed concrete pads on which they are installed. Carboline is deeply experienced in tank coatings and linings, and many of our Dudick concrete floor toppings would be suitable for secondary containment in CCS/CCUS facilities.
With so many applicable corrosion protection and secondary containment systems suitable for these environments, an owner or facility engineer’s best first step is to share specific site and environmental information when they consult with our technical service team.
Oxy-fuel combustion
Oxy-fuel combustion uses pure oxygen instead of normal air for combustion of the fossil fuel and produces a flue gas consisting mostly of CO₂ and water.
Incidentally, those are the ingredients for carbonic acid, which is aggressively corrosive. CO₂ and water can be separated in a cryogenic process, but that process has yet to reach industrial scale.
If and when it does, Carboline manufactures a variety of insulative coatings suitable for piping, ductwork, or structural steel in very cold or cryogenic environments. The following might be suitable:
Carbotherm 730 and Carbotherm 731 provide thermal protection down to -40°F (-40°C) and additionally are suitable as a base coat prior to application of fireproofing. Carbotherm 730 also is suitable at operating temperatures up to 175°F (79°C) while Carbotherm 731 is rated for service up to 302°F (150°C).
Thermaline 440 and Thermaline 450 EP each are suitable for cryogenic service down to -244°F (-153°C) and additionally are ideal for protection against corrosion under insulation (CUI) in wet-dry cycling service. These Thermaline products are suitable for high temperature service up to 400°F (204°C).
Here is an important caveat: Industry collaborators are still working out the ideal way to line piping or vessels that store materials at cryogenic temperatures. Super-cold conditions can embrittle steel, but not all liners are effective against H2. Its molecules are so small, they readily permeate most conventional linings.
Note also that corrosion is not the only risk to the longevity of equipment or the safety of those operating it. Passive fire protection is also necessary throughout CCS/CCUS facilities, and Pyrocrete 341 is unique in that it meets strict performance requirements for both high-temperature and cryogenic spill exposures.
Post-combustion capture
Post-combustion capture is the most common carbon capture technique and builds on the scrubbing technology that’s been widespread for decades. It is because of that longevity that coating manufacturers understand this carbon capture process better than the others.
The process utilizes an absorber which pulls in flue gas and exposes it to amine solvents to scrub the CO₂ out of it. Here’s a general walkthrough of the process including some coating or lining recommendations:
As with syngas production, the flue gas created immediately upon combustion is so hot that the ducting carrying it most likely will be made of a corrosion-resistant specialty alloy steel.
Next, if a plant burns coal, then a pre-treatment tower designed to scrub sulfur dioxide (SO₂) out of the gas stream is necessary. Plants burning natural gas probably won’t have SO₂ scrubbing towers.
After that, a gas stream encounters a CO₂ absorption and stripping stage which generates wet CO₂ gas at around 130°F (54°C). Carboline’s Plasite 4301 HT or Dudick’s Protecto-Coat 900HT are appropriate around that temperature. But processes surely vary, and in the event that this stage occurs at a higher temperature, consider Plasite 4300 or Plasite 4310. Each is rated for continuous service at 380°F (193°C) or maximum, non-continuous spikes of 460°F (238°C).
Areas within this stage may additionally be exposed to some abrasion because lean or rich amines are sprayed from their piping into reactors. Spray zone areas can be protected by abrasion-resistant Protecto-Line 900AR from Dudick. Some of the Carboline Plasite series products also feature abrasion resistance, and they may be applicable here depending on additional, more specific process conditions.
The absorption and stripping process introduces more heat, so the pure CO₂ plus some water that emerges from it might be at or above 300°F (149°C). Coatings and linings rated for higher-temperature service are named above. In some cases, though, this ducting might also be made of tile-lined concrete or specialty alloy piping.
Speaking of piping, at any CCS/CCUS process stage where an insulated pipe could be impacted by condensation owing to temperature differentials, a coating to resist corrosion under insulation (CUI) will be necessary.
Finally, protection will be needed for all the support tanks, secondary containment, and auxiliary piping carrying the amine solution for the solvent process. The conditions for the supporting equipment should be reviewed at the engineering stage to determine the correct lining system.
Carboline’s Semstone 870 aggregate-filled, glass mat-reinforced concrete or Dudick’s Protecto-Flex 900 are good candidates for secondary containment. Protecto-Flake 900 will serve well for primary storage of the amine, as would Semstone 870 without its glass mat reinforcement.
Where to go from here
CCS/CCUS will continue to evolve. Processes and equipment will change. That’s what makes now—and the near future—such an exciting time.
That’s also why stakeholders should not seek matter-of-fact CCS/CCUS corrosion protection prescriptions. Nothing is etched in stone at this early stage. Instead, they need asset protection partners who are strong in these two areas:
First, they need to know chemistry and corrosion principles. The use cases may be new and evolving, but when you know your chemistry, you can solve just about any problem.
And second, they need to have people and resources in place to create new products when existing technologies are not the right fit. That’s what happens every day in our Research, Development, and Innovation lab.